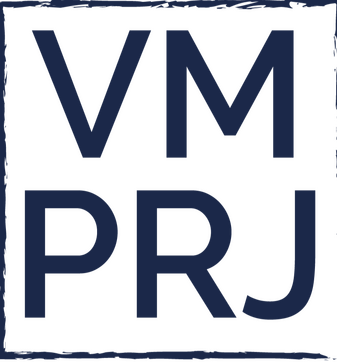
Work Smarter with Excel — Real-World Templates and Strategies
VivMo Projects, LLC
Discover clean, practical templates and expert strategies to turn Excel into your most powerful business tool.
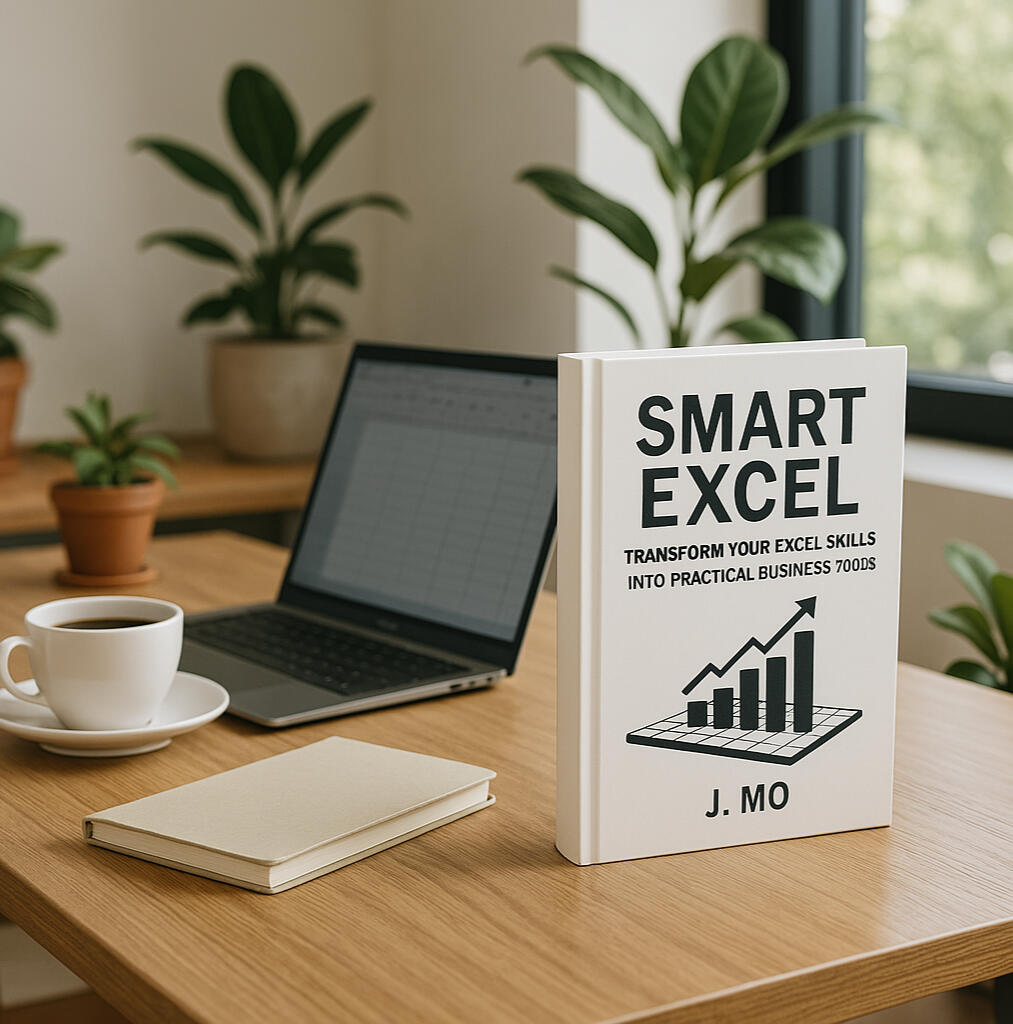
About us
At VivMoPro, we help professionals, managers, and entrepreneurs build smarter workflows through clean, functional Excel templates.
Inspired by real-world business needs, our designs follow the GFCR setup — ensuring clarity, consistency, and scalability in your work.
* Subscribe to learn more about this simple setup guide for FREE.
Start TODAY
Join Our FREE 52-Week Smart Excel Course
Learn practical Excel strategies every week, at your own pace.
Sign up now and get instant access to starter templates plus actionable lessons designed to boost your productivity and upgrade your professional skills — one step at a time.
BOOST YOUR PRODUCTIVITY
Shop
Excel Templates + Book
Explore our curated collection of ready-made Excel templates — project trackers, production planners, reporting dashboards, and more.
And now, discover Smart Excel — our practical guidebook designed to transform the way you use Excel in your business.
Thank you
Thank you for visiting VivMo Projects, LLC
— here’s to working smarter, one step at a time.
[ VivMo BLOG ]
Welcome to the VivMo Projects Blog — your guide to mastering Excel MRP, inventory management, and production planning.
Here, we share practical strategies, real-world examples, and professional insights to help you streamline your operations, plan smarter, and work more efficiently.
What is Tamaguri? A Simple Guide to Inventory and Production Planning in Excel
What is Tamaguri?
“Tamaguri,” also known as “Niguri,” is a practical tool used in Japanese manufacturing to simulate and plan materials and production. It’s designed to help planners and engineers understand when materials will run out and when to replenish — all through a simple yet powerful logic flow.
The Simple Logic Behind Tamaguri
At its core, Tamaguri is based on three fundamental concepts:
1) Inventory
2) Demand (inventory deduction)
3) Production or Purchase (inventory increase)
The calculation is straightforward:
Inventory after transactions = Starting inventory – Demand + Production/PurchaseThis cycle repeats over daily, weekly, or monthly timelines — giving you a clear picture of inventory flow across time.
🔍 Example:
Inventory at end of yesterday 500 pcs
Shipment (demand) today -100 pcs
Production/Purchase today +50 pcs
Inventory at end of today 450 pcs
With Tamaguri, this simple logic is extended across your planning horizon — whether it’s for a few days or several months — to help avoid shortages, reduce overstock, and improve ordering timing.
Need More?
If you're looking for more advanced versions or features like reorder points, lead time, and automatic ordering logic, feel free to explore our products or contact us — we’re here to help!
Understanding Manufacturing Capacity: A Practical Guide
In the realm of manufacturing and food service alike, understanding and calculating manufacturing capacity are essential for optimizing operations and meeting customer demand effectively. Let's explore the concept of manufacturing capacity using a real-world example of production in a factory.Imagine you're managing a manufacturing facility, and one of your key production processes involves assembling widgets. You know that manufacturing one widget takes about 5 minutes on average. With your factory operating for 8 hours a day, you calculate that within this time frame, you can theoretically produce a maximum of 96 widgets.Theoretical Capacity
= (Available Work Hours x 60) / Cycle Time
= (8ℎ × 60) / (5 minutes /widget) = 96 widgetsHowever, considering setup times, equipment maintenance, and other factors, you estimate that in reality, you can only produce about 80 widgets during those 8 hours.Actual Capacity
= Theoretical Capacity × Efficiency Rate
= 96 widgets × 83% = 79.68 widgets (rounded to 80 widgets)Now, let's consider the implications of this capacity calculation. As demand for your widgets grows, you realize that you need to produce 150 widgets per day to meet customer orders. However, based on your current capacity of 80 widgets per day, you recognize the need to increase your production capacity.Required Capacity = 150 widgets/day
Actual Capacity = 80 widgets / day
=> Need to double the production capacityIn response, you decide to invest in additional equipment and streamline your production processes to double your widget-making capacity, ensuring that you can meet growing customer demand while maintaining efficiency and quality standards.This example illustrates the importance of accurately assessing and optimizing manufacturing capacity to align with customer demand and business growth objectives. By understanding factors such as cycle time, available work hours, utilization rates, and efficiency rates, businesses can make informed decisions to enhance production efficiency, improve customer satisfaction, and drive sustainable growth. Whether you're managing a factory or a restaurant, mastering the art of capacity calculation is essential for achieving success in today's competitive marketplace.
Comparing MRP Calculation and Kanban Systems
Introduction
In the realm of manufacturing and inventory management, two prominent methodologies reign supreme: Material Requirements Planning (MRP) calculation and Kanban systems. While both approaches aim to streamline production processes and optimize inventory levels, they differ significantly in their principles, implementation, and suitability for various business environments.Let's delve into a comparative analysis of MRP calculation and Kanban systems to help you determine the right approach for your organization. Material Requirements Planning (MRP) calculation is a systematic approach to inventory management and production planning that relies on forecasting and demand projections to determine the quantity and timing of materials required for production. It utilizes mathematical algorithms and software systems to calculate material requirements based on factors such as lead times, order quantities, and production schedules. MRP calculation is well-suited for industries with complex production processes, high demand variability, and extensive supply chains, where accurate demand forecasting and precise inventory planning are essential for meeting customer demands while minimizing inventory holding costs.On the other hand, Kanban is a pull-based inventory management system that emphasizes visual signaling and just-in-time (JIT) production principles to control the flow of materials and goods throughout the production process. Originating from the Toyota Production System (TPS), Kanban utilizes visual cues, such as cards or bins, to signal when materials need to be replenished or production needs to be initiated. Kanban systems focus on reducing waste, optimizing workflow efficiency, and fostering continuous improvement by enabling teams to respond quickly to changes in demand and production requirements.
Limitations and Considerations
While both MRP calculation and Kanban systems offer distinct advantages, they also have their limitations and considerations:1. Complexity:
MRP calculation can be complex to implement and maintain, requiring sophisticated software systems and accurate demand forecasting to generate precise material requirements. In contrast, Kanban systems are simpler and more intuitive, relying on visual cues and decentralized decision-making to manage inventory levels and production flow.2. Flexibility:
MRP calculation provides greater flexibility in handling complex production processes and variable demand patterns, allowing for more comprehensive inventory planning and scheduling. Kanban systems are highly adaptable to changing production requirements and can quickly respond to fluctuations in demand, making them ideal for environments with volatile market conditions or rapidly changing customer preferences.3. Inventory Management:
MRP calculation excels in optimizing inventory levels and ensuring sufficient stock availability to meet production requirements and customer orders. However, it may lead to overproduction or excess inventory if demand forecasts are inaccurate or lead times are underestimated. Kanban systems focus on reducing inventory levels and eliminating waste by maintaining optimal stock levels and implementing pull-based production processes.4. Lead Time Management:
MRP calculation incorporates lead time considerations into its calculations to ensure timely procurement and production of materials. However, it may struggle to address variability in lead times or unexpected disruptions in the supply chain. Kanban systems emphasize reducing lead times and eliminating bottlenecks by fostering continuous flow and minimizing work in progress (WIP).
TextSuitability for Products/Processes
Kanban systems are particularly well-suited for managing more liquid materials such as resin, paint, and grease, where the loss or scrap of such materials is harder to control. These materials often have shorter shelf lives and require precise inventory management to prevent wastage and ensure product quality. Additionally, Kanban systems excel in environments with high product variety, frequent changeovers, and small batch sizes.On the other hand, MRP calculation is more suitable for products and processes where materials can be easily counted and managed, such as discrete manufacturing or assembly operations. It is ideal for industries with longer production lead times, higher demand predictability, and more stable supply chains. MRP calculation provides greater visibility into future material requirements and enables proactive planning and scheduling to meet production goals efficiently.
Conclusion
In conclusion, both MRP calculation and Kanban systems offer valuable tools for managing inventory and production processes, each with its own strengths and considerations. By carefully evaluating your organization's requirements and objectives, you can determine the most suitable approach to optimize your manufacturing operations and achieve sustainable business growth.
Lead Time
In the intricate dance of materials planning, one often-overlooked factor holds immense significance: lead time. From customs release delays to warehouse material preparation, lead time encompasses a multitude of internal and external variables that can significantly impact production schedules and inventory management. However, while meticulous consideration of lead time is essential for optimizing supply chain efficiency, it's equally crucial to strike a balance to prevent unnecessary inventory buildup.Lead time, the duration between the initiation and completion of a process, serves as a critical parameter in materials planning. It encompasses various stages within the supply chain, including procurement, production, transportation, and delivery. Each stage introduces its own set of lead time elements, which must be carefully analyzed and accounted for to ensure smooth operations and timely delivery of goods.One common pitfall in materials planning is overlooking the myriad factors contributing to lead time. External factors such as customs clearance delays, transportation disruptions, and supplier lead times can wreak havoc on production schedules if not adequately anticipated and managed. Similarly, internal factors like production setup times, material preparation delays, and quality control processes can introduce bottlenecks that impede workflow efficiency.To mitigate the risks associated with lead time variability, businesses must adopt a holistic approach to materials planning that encompasses both internal and external supply chain elements. This involves conducting comprehensive lead time analyses, identifying potential bottlenecks, and implementing strategies to streamline processes and reduce lead time variability. For example, establishing strong supplier relationships, implementing just-in-time inventory practices, and investing in advanced tracking and monitoring technologies can help minimize lead time uncertainties and improve overall supply chain resilience.However, it's essential to strike a delicate balance when considering lead time in materials planning. While it's tempting to err on the side of caution and overestimate lead times to buffer against potential delays, this approach can inadvertently lead to excessive inventory buildup and associated carrying costs. Therefore, it's crucial to continuously monitor and optimize lead time parameters to strike the right balance between ensuring supply chain resilience and minimizing inventory holding costs.In conclusion, lead time considerations play a pivotal role in materials planning, influencing production schedules, inventory levels, and overall supply chain efficiency. By meticulously analyzing and accounting for both internal and external lead time elements, businesses can mitigate risks, enhance operational agility, and maintain a competitive edge in today's dynamic marketplace. However, it's imperative to approach lead time optimization with a strategic mindset, balancing risk mitigation efforts with the need to minimize inventory holding costs and maximize operational efficiency.
Excel vs. SAP: Comparing Material Requirement Planning Solutions
In the realm of material requirement planning (MRP), businesses are faced with a crucial decision: whether to leverage the familiar capabilities of Excel or invest in established software solutions like SAP. Both options offer unique advantages and drawbacks, and understanding the differences is essential for making an informed choice. Let's dive into a comparison of the pros and cons of each approach.
Pros of Using Excel for Material Requirement Planning:
1. Cost-Effectiveness: Excel is often more cost-effective than dedicated MRP software like SAP. With Excel, businesses can avoid substantial upfront costs and ongoing licensing fees, making it an attractive option for small to medium-sized enterprises with limited budgets.
2. Flexibility and Customization: Excel provides unparalleled flexibility and customization. Users can tailor their Excel MRP templates to suit their specific needs, adjusting formulas, layouts, and functionalities as required. This level of customization allows businesses to create a solution that perfectly aligns with their unique processes and requirements.
3. Ease of Use: Excel is widely used and familiar to many employees, making it relatively easy to learn and use. Most users already have some level of proficiency in Excel, reducing the need for extensive training or specialized IT support. This ease of use can lead to faster implementation and adoption within the organization.
4. Accessibility: Excel files can be accessed and edited by multiple users simultaneously, enabling collaboration and real-time updates. Additionally, Excel files can be easily shared via email or cloud storage platforms, allowing team members to access critical MRP data from anywhere with an internet connection.
Cons of Using Excel for Material Requirement Planning:
1. Limited Functionality: While Excel offers a high degree of flexibility, it may lack the advanced features and functionalities available in dedicated MRP software like SAP. Excel may struggle to handle large datasets or complex calculations, leading to performance issues or errors in the MRP process.
2. Data Integrity Risks: Excel files are prone to errors, version control issues, and data integrity risks. Without proper controls and validation checks in place, there's a higher likelihood of inaccuracies in the MRP data, which can lead to costly mistakes in production planning and inventory management.
3. Scalability Challenges: Excel MRP solutions may struggle to scale alongside the business as it grows and evolves. As the volume and complexity of data increase, Excel files may become cumbersome to manage, leading to decreased efficiency and productivity.
Pros of Using SAP or Established MRP Software:
1. Advanced Functionality: Established MRP software like SAP offers advanced features and functionalities tailored specifically for material planning and supply chain management. These solutions may include robust forecasting algorithms, real-time inventory tracking, and integrated procurement and production planning modules.2. Enhanced Integration: SAP and other dedicated MRP software solutions offer seamless integration with other enterprise systems, such as accounting software, CRM systems, and ERP platforms. This integration streamlines data exchange and synchronization across different departments, improving overall operational efficiency and decision-making.3. Scalability: Dedicated MRP software solutions are designed to scale alongside the business, accommodating increasing complexity and volume as the organization grows. These solutions can handle large datasets, complex calculations, and multiple users simultaneously, ensuring reliable performance even in high-demand environments.
Cons of Using SAP or Established MRP Software:
1. Higher Costs: SAP and other established MRP software solutions typically involve significant upfront costs, licensing fees, and ongoing maintenance expenses. For small to medium-sized businesses with limited budgets, these costs may be prohibitive, making Excel a more attractive option.2. Learning Curve: SAP and other dedicated MRP software solutions often have a steep learning curve, requiring extensive training and specialized IT support for implementation and ongoing maintenance. This can lead to longer lead times for deployment and adoption within the organization.
3. Customization Limitations: While SAP and other established MRP software solutions offer robust features and functionalities out of the box, they may be less flexible and customizable compared to Excel. Businesses may need to adapt their processes to fit the capabilities of the software, rather than vice versa.
In conclusion, both Excel and established MRP software like SAP offer unique advantages and drawbacks for material requirement planning. While Excel excels in cost-effectiveness, flexibility, and ease of use, SAP provides advanced functionality, enhanced integration, and scalability. Ultimately, the choice between Excel and SAP depends on factors such as budget, company size, industry requirements, and long-term strategic objectives. By weighing the pros and cons of each approach, businesses can make an informed decision that aligns with their specific needs and goals.
BOM: Your Material Requirement Blueprint
In the complex world of manufacturing and production planning, the accuracy of material requirement calculations is the linchpin that holds everything together. At the heart of this accuracy lies a critical document known as the Bill of Materials (BOM). Whether you're using Excel-based systems or advanced solutions like SAP, the BOM is the foundation upon which precise calculations and efficient operations are built.
Understanding the Bill of Materials (BOM)
Before we dive into its importance, let's clarify what a BOM is. Essentially, a BOM is a comprehensive list of all the raw materials, components, sub-assemblies, and quantities needed to manufacture a finished product. It's a detailed recipe, a roadmap that guides the production process from start to finish.
The BOM's Role in Material Requirement Calculations
Regardless of the system you use, getting the BOM right is paramount. Here's a closer look at why:1) Data Integrity and Accuracy:
The BOM forms the core data set for material requirement calculations. Accurate and up-to-date BOMs ensure that your calculations are based on reliable information. Errors in the BOM can lead to costly miscalculations.2) Cross-Functional Collaboration:
To create an accurate BOM, collaboration is key. It involves various departments like engineering, production, procurement, and quality control. Each plays a role in verifying and updating BOMs to reflect real-world changes accurately.3) Version Control:
Changes in the BOM should be carefully documented, and everyone involved should have access to the most current version. This ensures that outdated or incorrect information doesn't find its way into the calculations.4) Continuous Review:
BOMs should be subject to regular reviews and updates to account for changes in product design, materials, or production processes. This continuous improvement process helps maintain accuracy over time.5) Data Validation:
Implementing data validation checks in the system can help ensure the integrity of BOM data. This can include checks for completeness, consistency, and adherence to predefined rules.6) Training and Documentation:
Properly training personnel involved in BOM management and documentation is critical. This helps reduce errors during data entry and ensures that everyone understands the importance of accurate BOMs.7) Integration with Systems:
Integrating BOM management with other systems, such as Enterprise Resource Planning (ERP) or Product Lifecycle Management (PLM) systems, can streamline the process and reduce the risk of data inconsistencies.8) Historical Data:
Maintaining historical BOM data is valuable for tracking changes over time and can be useful for auditing purposes.
Conclusion: The BOM's Crucial Role
In the world of manufacturing, the Bill of Materials (BOM) is far more than just a list of parts; it's a blueprint for precision. Excel-based systems or advanced ERP solutions like SAP rely on the BOM to calculate material requirements accurately. It's the bridge between your product design and the materials needed to bring it to life.Effective BOM management ensures that your material requirement calculations are not only precise but also adaptable to changes in design, materials, and production processes. It's the meticulous work that lays the foundation for streamlined operations, cost control, and ultimately, customer satisfaction. Remember, in the realm of material planning, "Garbage in, garbage out" holds true. Accurate input data, starting with the BOM, is essential for obtaining reliable output from any system.So, as you embark on your material planning journey, remember that success begins with a well-maintained and accurate Bill of Materials. It's the key to unlocking efficiency, minimizing costs, and ensuring your manufacturing process operates like a well-oiled machine.
Benefits and Drawbacks of Holding Safety Stock
In the intricate dance of inventory management, one term often takes center stage: safety stock. It's the safety net that businesses rely on to ensure they can meet customer demands in a world of unpredictable supply chains and fluctuating orders. Yet, like any strategic tool, safety stock comes with its own set of benefits and drawbacks.In this article, we delve into the world of safety stock, exploring how it can bolster your supply chain's resilience and customer satisfaction, while also examining the potential pitfalls that lurk in the shadows. Join us as we navigate the intricate balance between assurance and efficiency in inventory management.
Benefits of Safety Stock:
1. Buffer Against Variability: Safety stock acts as a buffer against unexpected fluctuations in demand or supply. It provides a cushion to absorb spikes in customer orders or delays in supplier deliveries, ensuring you can meet customer demands even in uncertain circumstances.2. Improved Customer Service: Having safety stock on hand enables you to maintain a high level of customer service. You can fulfill orders promptly, even when faced with unexpected disruptions, which enhances customer satisfaction and loyalty.3. Production Continuity: Safety stock plays a critical role in manufacturing by preventing production stoppages caused by material shortages. It also provides a valuable cushion against unexpected operational issues, such as machine failures or mold damage, ensuring your production lines stay active with minimal disruption.4. Supplier Reliability: Safety stock can reduce your dependence on supplier reliability. If a supplier experiences delays or shortages, you have a buffer of inventory to bridge the gap.
Drawbacks of Safety Stock:
1. Higher Holding Costs: Maintaining safety stock comes at a cost. You need additional storage space, which can lead to increased rent and handling expenses. Additionally, the capital tied up in safety stock could be used elsewhere.2. Risk of Obsolescence: If safety stock is not used within a reasonable time frame, it can become obsolete. This is especially true for products with limited shelf life or rapidly changing technology.3. Inventory Management Complexity: Safety stock adds complexity to inventory management. You must carefully monitor and adjust safety stock levels to avoid overstocking or understocking.4. Impact on Cash Flow: Holding excess inventory ties up capital that could be used for other investments or operational needs. This can affect your cash flow and liquidity.5. Reduced Inventory Turnover: Safety stock, if not managed properly, can lead to reduced inventory turnover. This means that products stay on the shelves longer, which can result in lower profitability.
In summary, safety stock plays a vital role in ensuring operational continuity and customer satisfaction by mitigating uncertainties in supply and demand. However, it should be managed carefully to strike the right balance between service levels and inventory holding costs. The benefits of safety stock are evident in its ability to maintain customer service and production efficiency, but the drawbacks should not be underestimated, as they can impact costs, cash flow, and overall inventory management complexity.
Mastering Material Planning with Excel MRP
When it comes to managing the intricate web of materials, production schedules, and inventory levels, precision is key. Whether you're a seasoned manufacturer or a startup trying to get a grip on your operations, Excel Material Requirements Planning (MRP) could be your secret weapon for success.
What is Excel MRP?
Excel MRP is a versatile tool that harnesses the power of Microsoft Excel to streamline your material planning process. It allows you to calculate the exact quantities of raw materials and components needed for production, helping you minimize waste, optimize resource allocation, and meet customer demand with ease.
Why Excel MRP?
1. Simplicity Meets Power: Excel MRP is a straightforward solution that packs a punch. It doesn't require complex software installations or extensive training. If you can use Excel, you can master Excel MRP.2. Adaptable Across Industries: Whether you're in manufacturing, retail, or the service industry, Excel MRP can be customized to suit your needs. It's the ultimate tool for businesses of all sizes and types.3. Cost-Effective: Excel MRP doesn't break the bank. It's a budget-friendly solution that delivers big on functionality. Say goodbye to expensive software licenses and hello to efficient planning.
How Does It Work?
Excel MRP works by pulling data from various sources, including your Bill of Materials (BOM), inventory levels, production schedules, and customer demand. It then crunches the numbers, providing you with a clear picture of what you need and when you need it.
Benefits of Excel MRP:
• Improved Efficiency: Streamline your operations by ensuring that you have the right materials at the right time.• Reduced Costs: Minimize overstock and understock situations, cutting down on excess inventory costs.• Enhanced Customer Satisfaction: Meet customer demand accurately, building trust and loyalty.• Optimized Resource Allocation: Allocate resources efficiently, making the most of your assets.
In Conclusion:
Excel MRP is not just a tool; it's your partner in material planning success. Whether you're looking to fine-tune your operations, minimize costs, or simply stay ahead of the competition, it's time to embrace the power of Excel MRP.Take control of your material planning today and unlock a world of efficiency and profitability with Excel MRP. Your journey to mastering material planning starts here.
© 2025 VivMo Projects, LLC. All rights reserved.